U Series Overview
For 30 years Ultra Motion has been a leading supplier of pressure-compensated oil-filled linear actuators for the most critical subsea applications. Our unique design allows for reliable actuation to depths greater than 6,000 meters below sea with self-compensation and an extremely small footprint. We offer the most cost effective PBOF solutions in the industry where power density, size, and reliability are critical.
The U-Series is an internally pressure-compensated oil-filled electromechanical actuator rated for operation to depths of 20,000 feet (6,000 meters). The U-Series has a variety of options including Nema 17 (U1) and Nema 23 (U2) stepper motors or brushless DC motors, self-locking Acme leadscrews or high efficiency ballscrews, in-line planetary gearheads, and strokes ranging from 1” to 16”. All U-series actuators come with an internal linear potentiometer for absolute position feedback, and will require external motor control electronics to operate. Please look into our AU Servo Cylinder product line if built-in control electronics are of interest.
Typical Applications:
Our submersible products are commonly used to operate hydroplanes on subsea vehicles, deploy instruments/accessories like float releases or sensors, raise masts/antennas on USVs, control hydrofoils or rudders on USVs, actuate subsea valves, and more.
Features:
- Pressure compensated oil-filled assembly with built-in compensator
- 6000+ meter operating depth (10,000 psi)
- Built-in linear potentiometer for absolute position feedback
- Stepper motor and brushless DC motor options
- In-line planetary gearhead options
- High efficiency ballscrew or self-locking Acme leadscrew options
- Peak forces up to 500 lbf
- Peak speeds up to 5 in/s
- 2”, 4”, 6”, and 8” strokes standard
- 1” to 16” strokes are available
- 0.005” nominal axial backlash
- -40°C to +60°C operating temperature range in air
- SubConn Wet-Mate connectors standard, custom cable lengths and outputs available.
Tech Specs
Stepper Motor
The Stepper Motor U-Series is the standard offering from Ultra Motion and is ideal for applications requiring high resolution positioning, high force at low speeds, and simple operation. The stepper motor U-Series requires external control electronics to operate the motor with at least 1.7 A_rms/phase current capability for the U1 and 4.2 A_rms/phase for the U2. All U-Series stepper motor actuators are wired in parallel by default. The user should account for headroom on performance to reduce the chance of stepper motor stall in the application.
Contact Ultra Motion engineering for actuator performance with planetary gearheads or for non-standard series wiring.
Note that the U-Series is rated for a mechanical maximum load of 500 lbf. The performance shown in the graphs above represents the continuous capability in air using an Applied Motion stepper motor controller
Brushless DC
The brushless DC motor options for the U-Series offer higher dynamic capability and performance over a larger range of speeds when compared to the stepper motor actuators. The BLDC U-Series include Hall effect sensors for commutation and will require external BLDC drive electronics to operate. The coarse Hall effect commutation feedback makes the BLDC U-Series less suitable for high resolution positioning applications, but the increased dynamic capability makes them useful for control surfaces on subsea vehicles. The closed loop commutation also makes the BLDC U-Series important for applications that can have large peak hydrodynamic load scenarios where an open-loop commutated stepper motor may lose synchronization and stall. Linear potentiometers are standard on all U-Series actuators
Planetary gearheads can be incorporated into the BLDC line of U-Series actuators allowing for high force, low speed, closed loop commutated actuation.
As in all applications, avoid contacting the internal mechanical hardstops of the actuator. Driving into external/internal mechanical hardstops with a BLDC actuator can lead to overheating of the motor if the control electronic’s current limit is set above the continuous current rating of the actuator.
The continuous force in these performance graphs represents the load at which 100% duty cycle is allowable in air. The peak force is set to twice that of the continuous force as a reference.
U-Series
Customizations available.
Contact Ultra Motion engineering.
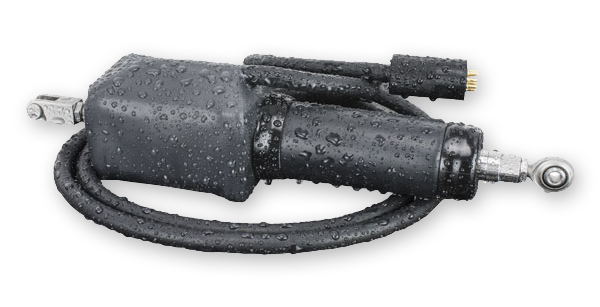
"*" indicates required fields