The Industrial
servocylinder
Series A2
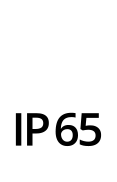
The A2 Industrial Servo Cylinder is designed to excel in industrial/harsh environments where exposure to dirt, liquids, washdown, or other demanding conditions may be expected. The A2 Industrial Servo Cylinder makes use of the same robust control electronics and drive components as the A1, but includes several upgrades to increase its environmental ruggedness. Upgrades include:
The A-Series Servo Cylinder is a rod-style, brushless DC electromechanical actuator with built-in controller and Phase Index® absolute position sensor. Providing up to 530 lbf peak force and up to 7.75″ of travel, the Servo Cylinder was designed from the ground up to be extremely robust and very simple to use. After a simple USB configuration, power and signal are the only connections required to operate the Servo Cylinder.
Ultra Motion’s Phase Index® is seamlessly integrated into the Servo Cylinder. It provides absolute, digital position feedback of the actuator throughout the entire stroke and is also used for Field-Oriented Control of the brushless motor. Besides Phase Index®, no sensors are required to provide absolute position feedback of the actuator shaft and the BLDC rotor. The need for a linear potentiometer, LVDT, limit switches, 6-step hall sensors, incremental encoder, or resolver is eliminated. Simplifying the actuator system in this way greatly improves reliability, increases the operating temperature range, and reduces overall cost.
The Servo Cylinder comes in two motor stack sizes (100W and 180W) and can be configured with a high efficiency ball screw or a self-locking acme leadscrew.
Force: Up to 270 lbf continuous, 530 lbf peak
Speed: Up to 14 in/s
Linear resolution (with acme screw): 0.000061″ (1.55 µm)
Operating Voltage Range: 8-36 VDC
Stroke Lengths: Up to 7.75”
Phase Index® is Ultra Motion’s innovative new position sensor technology for electromechanical actuators. The Phase Index® position sensor is a digital, high-speed, high-resolution, non-contacting actuator position sensor that works over a wide temperature range and is resistant to vibration, shock, particulate debris, and condensing moisture. The sensor is self-calibrating, and does not need backup power to retain absolute position when power is off. The absolute position of an actuator is available immediately upon power-up and with full accuracy. No power-up homing routine is needed to establish an accurate absolute position.
The first commercial implementation of Ultra Motion’s Phase Index® position sensor technology, used in a demanding aerospace application, has performed flawlessly through extensive and rigorous environmental testing and field operations. Ultra Motion is now adapting this proven sensor technology to a range of designs from high-performance, high-power-density aircraft actuators, to low-cost industrial motion control. Phase Index® actuator position sensing technology is available exclusively from Ultra Motion, so contact our engineers to find out how it can work for your application.
The Phase Index® position sensor works by using the phase relationship between two cyclic signals with different periods to determine absolute position within a larger interference cycle of the combined signals. When implemented with state-of-the-art magnetic sensor technology, this technique allows for a high-speed, high-resolution, digital actuator position sensor that is always accurate and that works across a range of harsh environmental conditions.
The Servo Cylinder has an RS-232 serial command line interface (CLI) that offers the user complete control over all performance parameters, motion commands, and diagnostic information.
The Servo Cylinder can be controlled through a terminal program such as PuTTY, a PLC, or any program that can control a serial communication port such as LabVIEW, MATLAB, etc.
The Servo Cylinder can be configured to operate in “Human mode” where detailed information regarding commands and asynchronous error messages are output to the terminal window. The Servo Cylinder can also be set to operate in “Machine Mode” where asynchronous messages are turned off, and checksums are sent to ensure communication integrity.
Proportional modes take full advantage of the benefits that the integrated Phase Index® absolute position sensor has to offer. The user simply supplies a signal proportional to the desired position, and the Servo Cylinder immediately responds.
There is no homing required so the user does not have to worry about intermittent power interruptions causing downtime or failure of their machine due to loss of position.
Software definable end-of-stroke limits eliminate the need for limit switches.
The user simply configures the stroke range, and the corresponding proportional input signal range, and the Servo Cylinder is ready to use.
Voltage Min | Voltage Max | Position Min | Position Max |
---|---|---|---|
-10V | +10V | Full Retract | Full Extend |
0V | +5V | 2.000″ | 3.125″ |
-5V | +5V | Full Retract | 1.500″ |
Current Min | Current Max | Position Min | Position Max |
---|---|---|---|
4 mA | 20 mA | Full Retract | Full Extend |
4 mA | 16 mA | 2.000″ | 3.125″ |
10 mA | 20 mA | Full Retract | 1.500″ |
Pulse Min | Pulse Max | Position Min | Position Max |
---|---|---|---|
1 ms | 2 ms | Full Retract | Full Extend |
1.2 ms | 1.8 ms | 2.000″ | 3.125″ |
1.5 ms | 2 ms | Mid Stroke | Full Extend |
Incremental input modes allow for many users to realize the benefits of the Servo Cylinder without upgrading their existing control system or PLCs. The Servo Cylinder will provide high performance BLDC actuation using the following as position commands:
As with all operating modes, there is no homing required. The absolute position of the actuator can be read via the RS-232 Command Line Interface, or output as a 1 kHz PWM waveform from one of the Servo Cylinder’s output pins.
Software definable end-of-stroke limits eliminate the need for limit switches.
This mode allows the Servo Cylinder to behave as a drop-in replacement to stepper motor systems while providing higher efficiency, increased torque at high speeds, no lost steps or stalling, and smoother operation in an integrated package.
The configurable GPIO can output a PWM signal proportional to the absolute position of the Servo Cylinder, or the absolute position can be read directly over serial, eliminating the need for homing and external absolute position sensors.
Two high speed optically isolated digital inputs reject noise and provide robust communication between PLCs and the Servo Cylinder.
The Servo Cylinder mimics the simplicity of a brushed DC control system with the added performance benefits of a high efficiency, long life BLDC motor.
The actuator immediately responds to a user supplied extend/retract signal sent to the optically isolated digital inputs.
The absolute position capability of the Servo Cylinder eliminates the need for external limit switches and also allows for user configurable acceleration and max velocity for smooth, controlled motion.
Speed or Torque can be controlled by using one of the Servo Cylinder’s analog inputs.
Four Preset position mode provides the user with an easy way to perform a variety of positioning tasks. The user selects one of four pre-configured position by toggling the state of the two optically isolated digital inputs (00,01,10,11), causing the actuator to move to the selected position using the Servo Cylinder’s built-in trajectory generator.
Homing is not required, which increases the ease of integration into machines and reduces complexity.
A user defined input filter is available to reject noise and debounce mechanical switches.