- Integrated BLDC control electronics.
- Contactless absolute position feedback.
- Easy configuration and multiple communication protocols.
Features & Ratings:
- Integrated Controller: Input a compatible control signal for operation
- Absolute Encoding: No homing/battery required
- Full Command Line (CLI) language: For control, feedback, and communication
- Easy Configuration: Configured via editable text file in USB Mass Storage, or with serial
commands
Rating | Value |
Force (Peak) | Up to 530 lbf (2.36kN) |
Force (Continuous) | Up to 270 lbf (1.20kN) |
Speed | Up to 14in/s (356mm/s) |
Stroke Length | Up to 7.75in (197mm) |
Resolution | Up to 0.000061in [1.55µm] |
Operating Voltage | 8 to 36 VDC |
Ingress Protection | IP50 to IP68 (Varies by Model) |
Temp. Range | -40°F to 176°F [-40°C to 80°C] |
The A-Series Servo Cylinder is a rod-style, brushless DC electromechanical actuator with built-in controller and Phase Index® absolute position sensor. Providing up to 530 lbf peak force and up to 7.75” of travel, the Servo Cylinder was designed from the ground up to be extremely robust and very simple to use. After a simple USB configuration, power and signal are the only connections required to operate the Servo Cylinder.
Ultra Motion’s Phase Index® is seamlessly integrated into the Servo Cylinder, which provides absolute, digital position feedback of the actuator throughout the entire stroke and is also used in Field-Oriented Control of the motor. Besides Phase Index®, no sensors are required to provide absolute position feedback of the actuator shaft and the BLDC rotor, which improves reliability.
- No homing required
- No limit switches
- No potentiometer wear
- No sensor noise
- No battery required to maintain absolute position
The Servo Cylinder comes in two motor stack sizes (100W and 180W) and can be configured with a high efficiency ball screw or a self-locking acme leadscrew.
Integrated Controller Options:
Control Modes & Features | Classic ControllerOption Code “N” | Industrial ControllerOption Code “P” | CAN ControllerOption Code “C” | Deepsea Controller Option Code “Q” |
---|---|---|---|---|
RS232 Serial w/ Command Line Interface (CLI) |
0
|
|||
RS422 Serial (Full-Duplex, 4-wire) w/ Command Line Interface (CLI) |
0
|
0
|
||
RS485 Serial (Half-Duplex, 2-wire) w/ Command Line Interface (CLI) *Does not command motion |
0
|
* | ||
CAN 2.0B (Configurable Protocol) |
0
|
0
|
||
CANopen (CiA DS301, CiA DS402) |
0
|
|||
Analog Voltage (-10 V to +10 V) Control |
0
|
0
|
||
Analog Current (4-20 mA) Control Input |
0
|
0
|
||
Isolated Analog Current (4-20 mA) Output (Configurable Data Source) |
0
|
|||
1-2 ms Pulse (RC PWM) |
0
|
* | ||
Toggle (Simple On/Off for Extend/Retract) Control |
0
|
|||
Pre-set Position Control |
0
|
* | ||
Isolated Digital Inputs | 2X | 1X | 3X |
0
|
Transient Voltage Protection on Signal Lines |
0
|
0
|
0
|
|
Deepsea Operation to 6,000 meters (10,000 PSI) *AU Series Only |
0
|
* : Contact Ultra Motion to discuss this feature.
Parallel Mount Linear Actuators
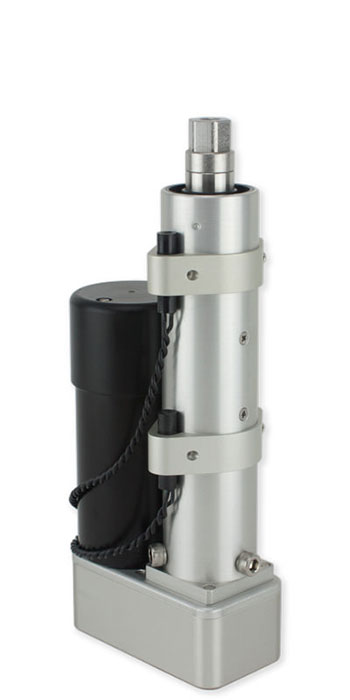
- Smallest reverse parallel mount actuator offered by Ultra Motion.
- Very high power density, ideal for weight and size constrained applications such as aerospace and robotics.
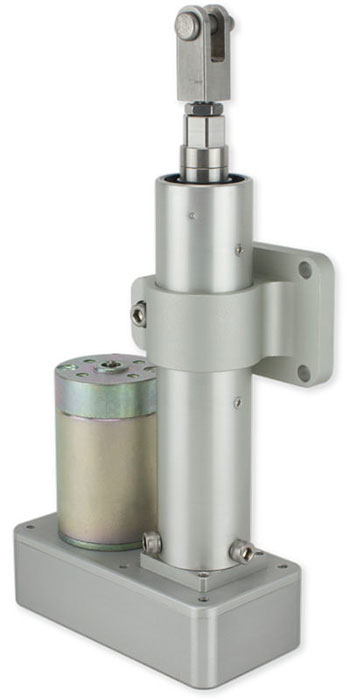
- Fits NEMA 17 frame motors and a variety of DC brushed motors.
- Ideal for high performance, long life, economical actuation systems.
- Timing belt ratio up to 5:1
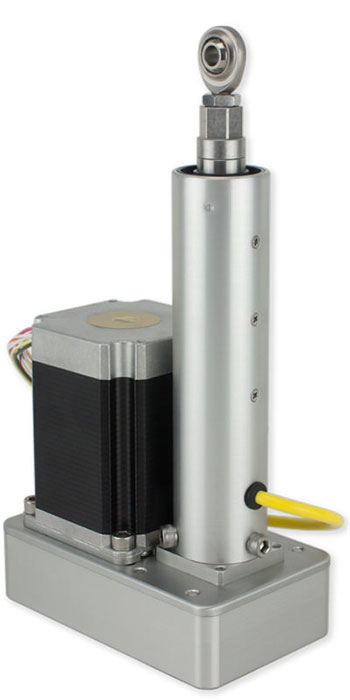
- Fits most NEMA 23 frame motors.
- Timing belt ratio up to 4:1
- Extends speed and force capability of Series B2.
In-line Linear Actuators
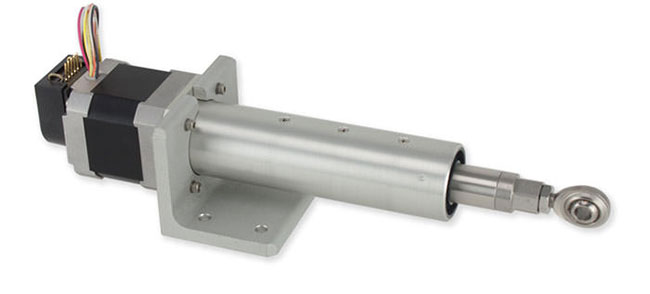
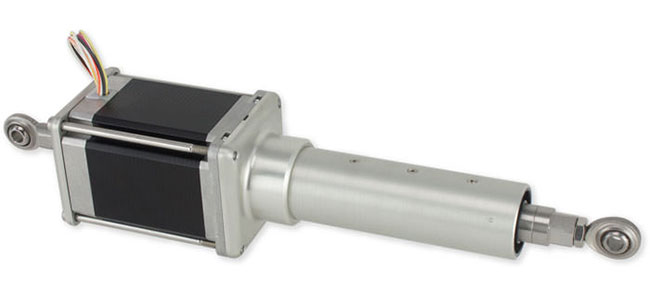
- NEMA 23 frame size
- Capable of up to 450 lbs of force
Integrated Linear Actuators
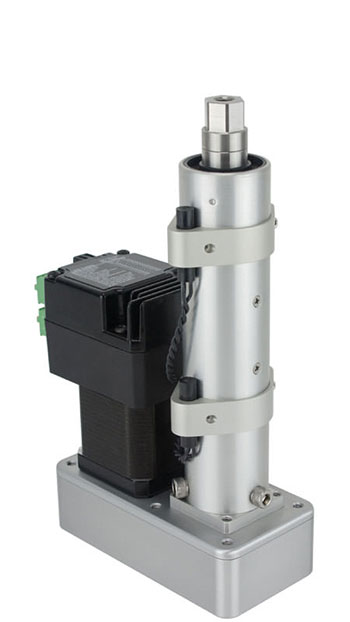
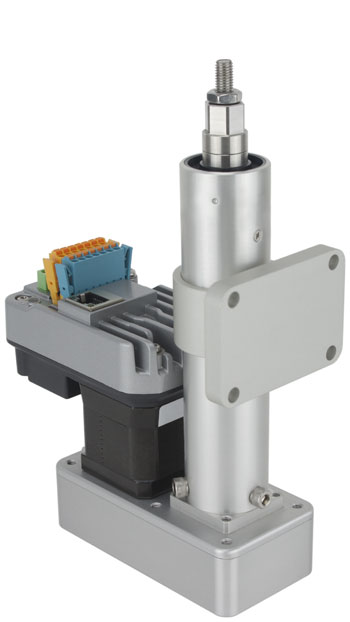
Integrated Steppers
- Using internal encoders, integrated stepper motor actuators achieve enhanced performance, higher efficiencies and prevent loss of synchronization (stall).
- The I1 series of actuators are programmable and can be configured to operate with CANopen, Ethernet, Profinet, and step and direction systems.
- We offer Lexium MDrive and Applied Motion NEMA 17 and NEMA 23 frame size integrated stepper motors with our actuators.
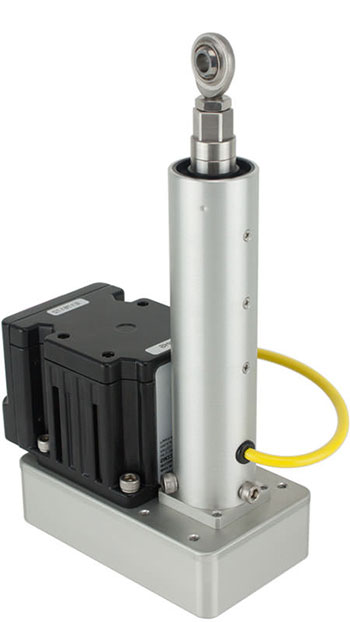
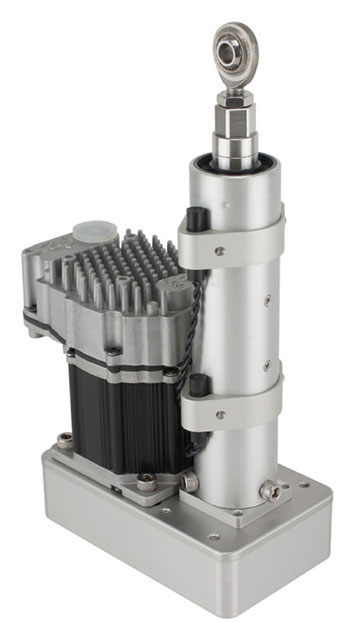
Integrated BLDC
- We offer ClearPath motors on our actuators for a high power density, simple to use actuator ideal for digital systems and BLDC replacements to existing Stepper Motor systems. These actuators have built-in limit switch and hardstop homing routines.
- We also offer NEMA 17 and NEMA 23 Smart Motors, which offer full programmability, analog signal compatibility, and industrial network protocols such as CANopen and Ethernet. These actuators can be programmed for limit switch homing, hard-stop homing, or for motionless homing using Ultra Motion’s internal potentiometer.
Underwater Linear Actuators
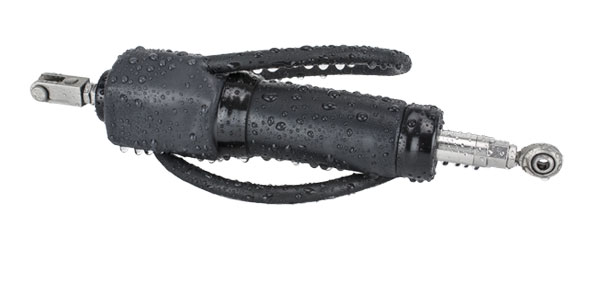
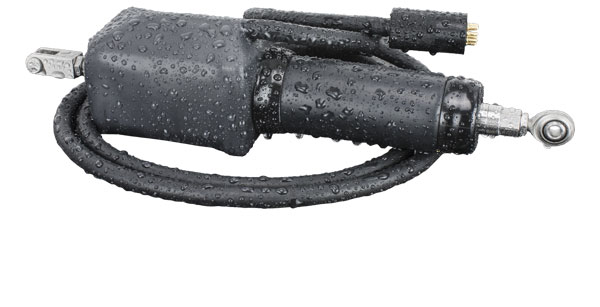
- NEMA 23 frame size
- Capable of up to 450 lbs force
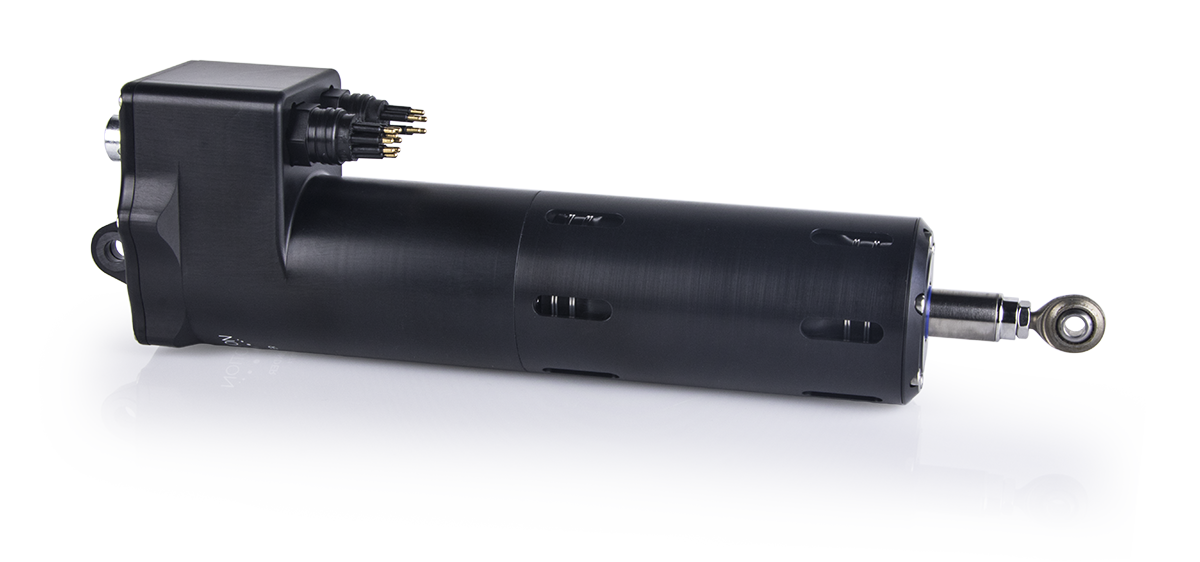
- Forces up to 530 lbf
- Speeds up to 14 in/s
- Strokes up to 7.75 inches
Specialty Linear Actuators
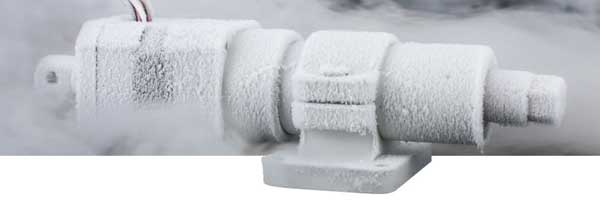
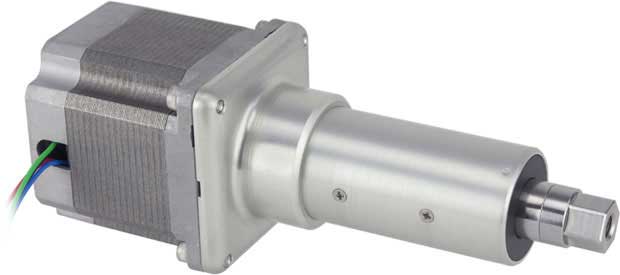
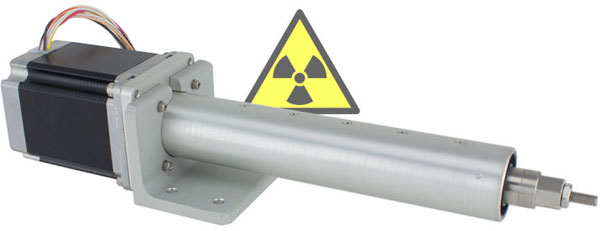
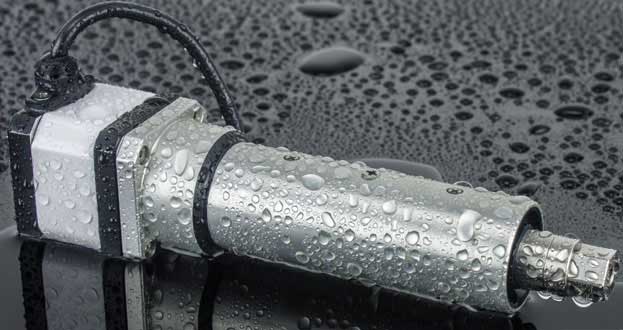