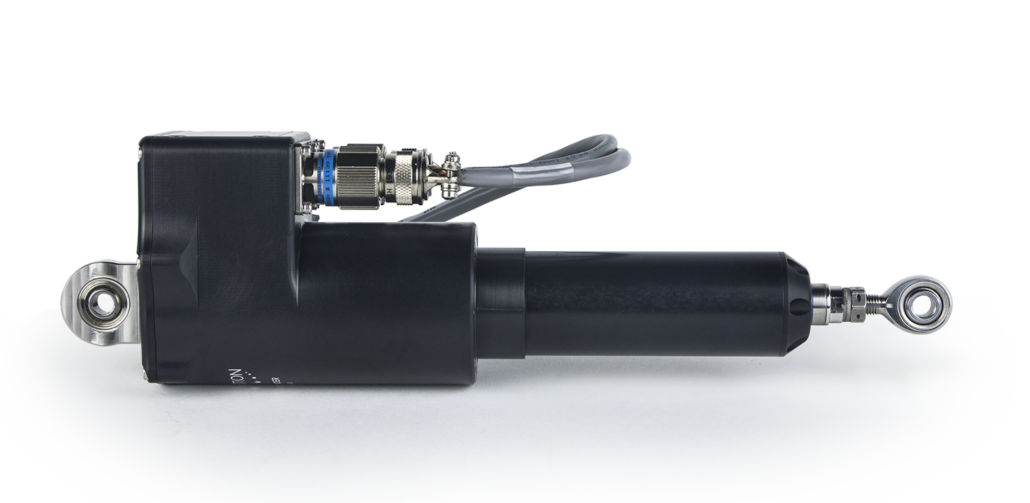
The Servo Cylinder is a popular choice for high reliability UAV control surface and utility linear actuator applications. The A-Series Servo Cylinder uses a brushless DC motor and contactless absolute position feedback to reduce wear and provide superior performance when compared to potentiometers and brushed DC solutions. The built-in control electronics offer a variety of communication interfaces including CAN 2.0B, RS-422/485 serial, RC PWM, 4-20 mA in/out, etc.
The Ultra Motion AM Servo Cylinder is designed to excel in harsh shock/vibe environments with IP65 dynamic and IP67 static ingress protection ratings. The D38999 receptacles provide military standard connections, and the on-board temperature, current, voltage, and humidity sensors allow for constant health monitoring of the servo actuator. Custom heater firmware is available that maintains a configurable controller temperature even in ambient environments < -40°C. The Servo Cylinder has an 8 to 36 VDC operating bus voltage, which is compliant with the majority of UAV power busses and will survive at >51 VDC.
The Servo Cylinder offers forces up to 530 lbf, strokes up to 7.75 inches, and speeds up to 14 in/s, allowing for high bandwidth control >15 Hz at small position amplitudes.
The Servo Cylinder uses a helically skewed BLDC motor to eliminate detent torque which allows for smooth backdriving at low forces (~10 lbf) when unpowered or commanded to zero phase current. This allows for the possibility of eliminating bulky and costly magnetic clutch assemblies from the actuator in optionally piloted vehicle (OPV) applications.
Conversions of control surfaces from rotary actuators to linear actuators can lead to increased power density, increased control authority due to higher resolution position control and significantly reduced backlash, and decreased cost/mass. Contact Ultra Motion Engineering to discuss your unmanned vehicle actuator requirements in detail. View Servo Cylinder performance and dimensions by using our online configurator here.